
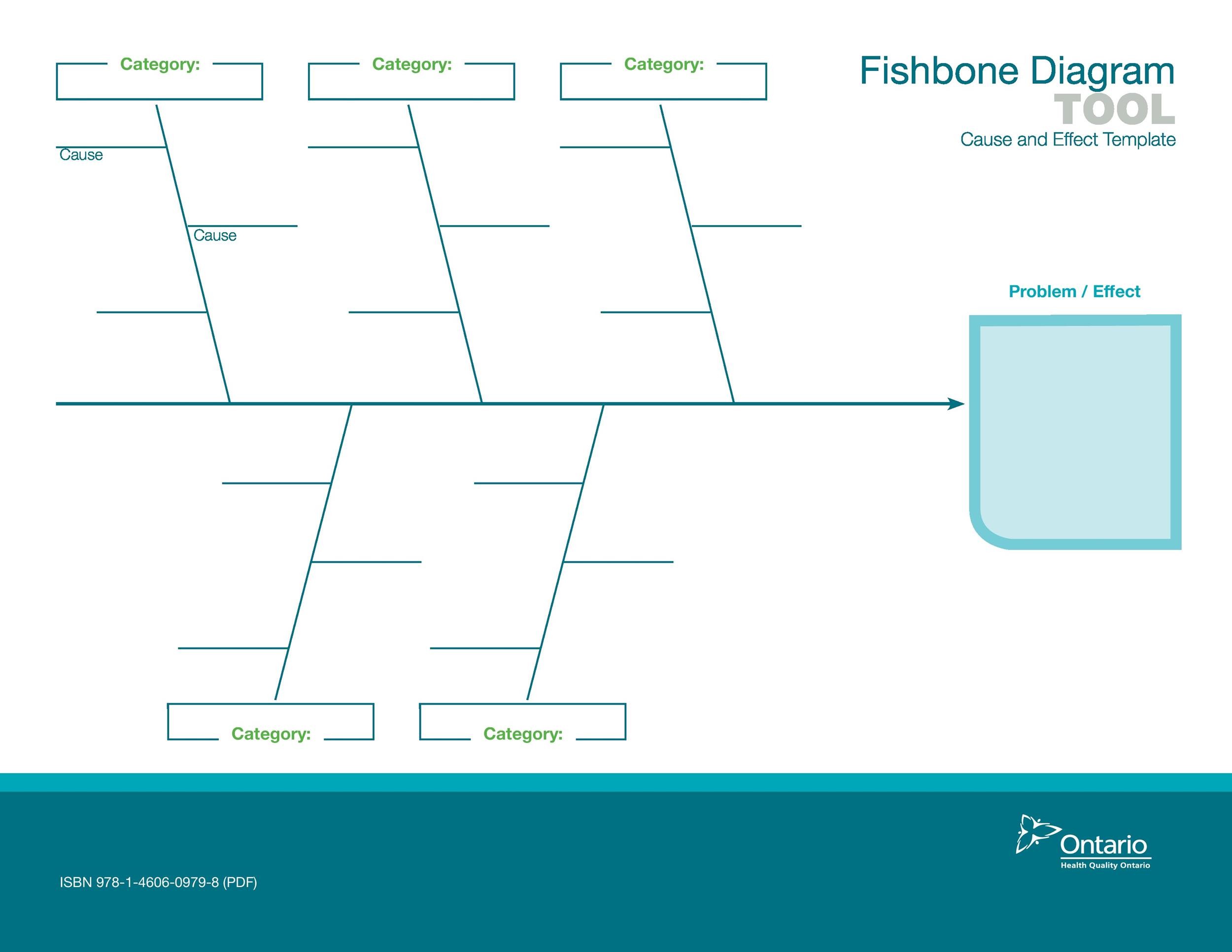
- #No problems ishikawa diagram series#
- #No problems ishikawa diagram download#
- #No problems ishikawa diagram free#
It leaves everything open to be specific to the topic at hand. the team starts by thinking of their own categories. Rather than starting with the method, materials, etc. This version doesn’t have any predetermined categories, so it is the most flexible. Here are a few more you may find helpful. It covers all the major aspects we come across in a manufacturing setting. Most of the time, manufacturing teams will use these six categories in their Fishbone Diagrams: Machine, Methods, Measurements, Materials, Manpower, and Environment. Existing types of Fishbone Diagrams 5M/1E (Standard Manufacturing) Fishbone Diagram
#No problems ishikawa diagram free#
Canva, a free graphic design platform, will also help you make a Fishbone Diagram in exchange for your email address.
#No problems ishikawa diagram download#
Scroll to the bottom of that page to download the Excel template. ASQ also offers a Fishbone Diagram builder to make the setup process easier. There are the variations that can tailor the cause and effect diagram to your specific situation.

Along the way, you may also discover other issues or causes for other effects. Eventually, you’ll come up with the root cause. This helps you narrow the possibilities to a list of most likely causes and test from there.
#No problems ishikawa diagram series#
Once you’ve added enough data to be helpful, dive into evaluating each one with a series of questions – Why’s. how the problem is showing up on the manufacturing floor). Each branch is a category.įor each category, brainstorm specific things that could be causing the effect, or symptom (i.e. It’s called a Fishbone Diagram, because it looks like a fish skeleton with the symptom, or effect of the cause, as the head and potential causes branching out from the spine. It is used to first brainstorm the potential causes of a problem, then narrow potential causes to find the root cause and move on to a solution. The Fishbone Diagram is also known as the Cause and Effect Diagram, C&E Diagram, or the Ishikawa Diagram, named after its inventor Kauoru Ishikawa, organizational theorist and engineering Professor at The University of Tokyo. The key is to choose the one that best fits the problem you’re addressing. Simple as it may be, even the fishbone diagram has several different structures for different purposes. There are many ways to do this and the Fishbone Diagram is one of them. Soon after, you’ll need to identify the cause. To use the Ishikawa diagram you must first choose a problem of any nature such as an audit, a claim from a customer, or a technical issue and place it at the right end of the spine, as indicated in the following image.Identifying a problem is just the beginning. This scheme helps identify the main and secondary issues that contribute to the issue in question. The word fishbone comes precisely from its presentation format, made from a central unifying line that leads all potential causes, represented by the lateral spines, to a single effect. It is important to emphasize that identifying proper and efficient solutions is a challenging task that we see many organizations struggle with. Its efficiency lies, among other factors, in allowing employees to avoid solutions that fix the problem peripherally and not thoroughly. This tool aims to identify the root cause of a problem through a visual categorization of its potential causes. The Ishikawa diagram, also known as fishbone or cause and effect diagram, was first applied in 1953 in Japan by one of the greatest pioneers in quality control within organizations, Kaoru Ishikawa.
